Quick Guide to Wood Joinery
The world of woodworking joinery can be overwhelming, with joints that range from simple to complex, traditional to novel.
There are lots of ways to approach this huge topic. A good way to start is to divide joinery into two groups: cabinetry joinery and furniture joinery. By cabinetry, we mean cabinets that attach to the wall in some way. And by furniture, we mean free-standing pieces. That difference means a lot.
While built-ins gain support from walls and floors, free-standing furniture is self-supporting, and thus needs stronger joints. Keep these two categories in mind as we run through the most common joints below.
Fast and easy joints
Until you own Shaper Origin—and can machine even the trickiest joints in a fraction of the usual time—fast and easy joinery usually means not quite as strong. And that’s just fine for a lot of tasks.
For all of the following, all you have to do is cut square ends on your parts—called butt joints—and the joinery system takes over.
Glue is the most basic joinery system
In some cases, glue (and clamp pressure) are all you need to make a strong joint. There are two keys to success when building these panels. First, the mating surfaces must be flat, straight, and clean. Second, the clamp pressure must be strong and consistent along the length of the whole joint.

Inspect the interlocking joints featured later in this article, and you’ll find several joints that are held together by only wood and glue. These joints typically have two things in common - plenty of surface area, and support from long, unbroken wood grain. Take a close look at most butt joints, however, and you’ll see that end-grain is involved. Joints involving end grain typically have low surface area or discontinuous wood grain, and so these joints typically require reinforcement.
Screws can help
The simplest way to reinforce a butt joint is the humble wood screw. Executed properly, a screw acts like a metal dowel, and can be extremely strong. One key is creating a clearance hole in the piece being attached, so only the head of the screw pulls down on it. In most cases, you also want a pilot hole in the piece you are attaching to. The clearance hole is just larger than the overall diameter of the threads, allowing them to pass through freely; and the pilot hole is roughly equal to the small diameter between the threads, allowing the threads to grab without splitting the wood.
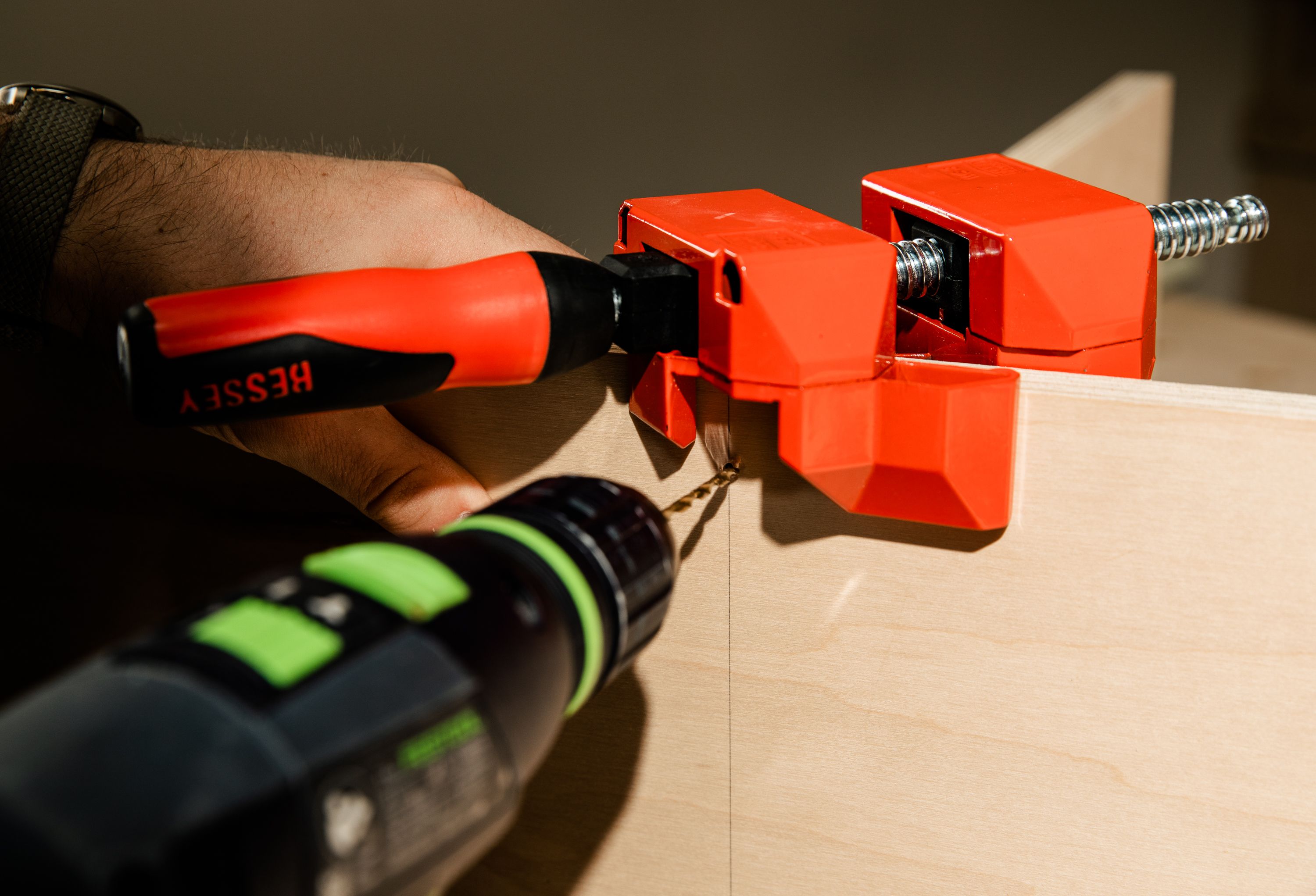
For a clean appearance, you can counterbore your screw heads, setting them deep into the wood, and then fill those holes with a wood plug. For projects needing less refinement, you can simply let the heads show. In some cases the screw heads will even be hidden naturally as your work is assembled , as on a row of cabinets joined together side to side.
Pocket-hole screws work from the inside out
Pocket-hole joints offer one of the best combinations of strength, speed, and versatility, which is why they are so popular for built-in cabinets. The difference between a traditional screw and pocket-hole screw is how the fasteners pass through the parts. Pocket screws work in the opposite direction of a typical wood screw: starting from inside a cabinet or the backside of a face frame, for example, passing through the end grain, and screwing into the long grain of the mating part, grabbing across the grain for a tighter grip. This has two advantages: strength and appearance.

If you were screwing those same cabinet parts together in the usual way, outside-in, the screws would be passing into end grain, where they don’t tend to grab as well. And because of the way pocket-screws enter the parts, inside-out, the entry holes are easier to hide.
To drill pocket holes, you need a pocket-hole jig, but effective ones are relatively inexpensive. The real downside is the unsightly holes. But if you can hide them, this joint is super quick and surprisingly strong.
Biscuits align and strengthen
A biscuit is a small pressed plywood wafer, sized to fit slots you cut quickly and accurately with a small power tool called a biscuit joiner. Push your parts together, make little tick marks across them where you want the biscuits to go, and the biscuit joiner cuts matching slots in seconds. The other cool thing about biscuits is how they swell up and tighten after glue is applied, completing a powerful system.
As handy as biscuits can be, they don’t go very deep into the wood, so they tend to get used more in built-in cabinetry. In free-standing furniture, biscuits are used as much for alignment as strength, like when joining a bunch of boards side-to-side to create a tabletop.
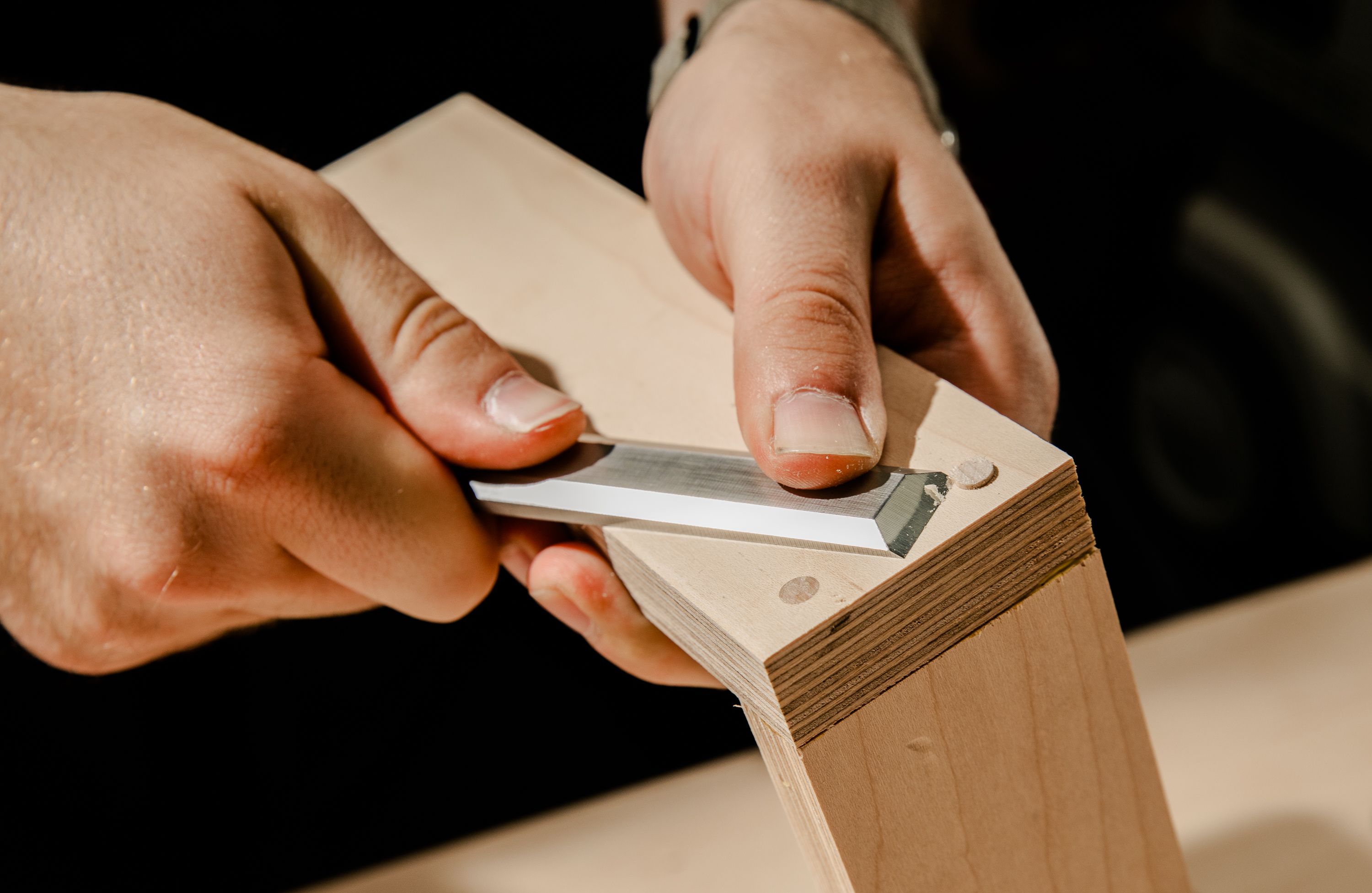
Dowels are stronger, but tricky
Quick, versatile, and strong, dowels are often overlooked as a joinery system. Variations of wood pegs have been used for centuries to join wood pieces. Dowels are wood pegs that are machined round, letting them slip perfectly into drilled holes; if you can drill a hole, you can insert a dowel. Drill matching holes in two mating pieces of wood, insert some glue and a dowel, and you have a powerful joint.
The trick is making the mating holes align perfectly, and for that there are a host of handy little jigs that work with your cordless drill. You can also make your own doweling jigs, by drilling holes in a plywood template, letting you drill a whole row of dowel holes in one shot.
The fussiness of dowel alignment multiplies across a large project, so dowel joinery is better suited for work of moderate size. But other than chairs or very large dining tables, dowels will let you build a houseful of furniture using just a drill and a simple jig.
Festool’s Domino system is fast, strong, and easy
Tenon is a traditional term for a rectangular protrusion on the end of a board, which fits into a rectangular hole in a mating piece, called a mortise. Tenons have a large surface area for glue application, and you can make them as large and deep as your pieces will accommodate. These two factors make the mortise-and-tenon the most powerful joinery system that exists.
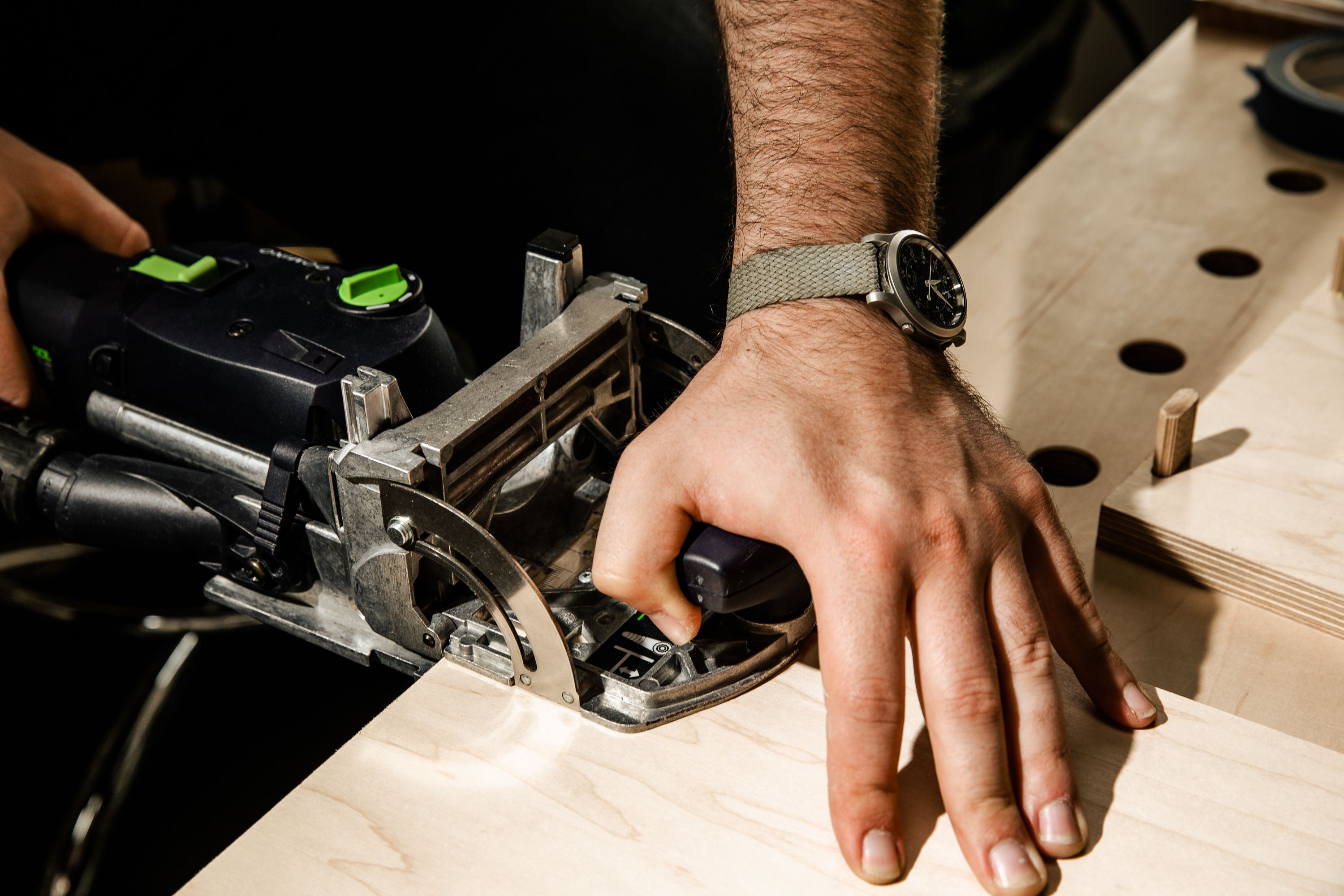
We’ll go deeper into the mighty M&T below, but we mention it here to talk briefly about the Festool Domino, a tool that works like a biscuit joiner but cuts mortises instead of shallow biscuit slots. Better yet, the kit includes a range of premade tenons (those are the “Dominoes”) that fit those mortises perfectly. All you have to do is cut an accurate butt joint, and in a few minutes the Domino joiner can add mortises and tenons that are both stronger and easier to align than dowels, thanks to the flexibility of the Domino joiner’s alignment system and the large glue surface of the Dominoes themselves.

Miters are another form of butt joint
Cut off the ends of two boards at an angle, usually 45 degrees, and you have a miter joint. Because the 45-degree surfaces are a hybrid of end and long grain, their strength is limited with glue alone. So while miter joints might be fine on their own for picture frames and other light-duty applications, they need reinforcement to withstand serious stresses, including the way wood expands and contracts in different seasons.
Another version of the miter travels along the long edges of a board—to create hollow columns and such. Being long-grain-to-long-grain, these types of miters are much stronger and usually do not require reinforcement. That said, biscuits or splines are often inserted to keep the parts aligned during assembly.
Simple interlocking joints
We’ve arrived at the traditional, interlocking wood joints. They are thought of as traditional because they’ve all been around for centuries, and have withstood the toughest test of all: time. The key to all of them is some sort of interlock. In other words, all include some sort of mating parts that make the joint mechanically strong even without glue added—although a little glue is always helpful.
Rabbets, dadoes, and grooves
Some of the most basic interlocking joints are square tongues and grooves. While all related, these joints come with confusing terminology.
If you cut a square notch along the end or side of a piece, you’ve cut a rabbet (or rebate, for those across the pond). Cut those along both sides of that edge or end, and you’ve formed a tongue.
The mating part of those rabbets and tongues is a square slot of some kind. Confusingly, where you cut these slots changes their name. Cut the slot across the grain—to hold shelves in the sides of a cabinet, for example—and it’s called a dado. Cut it down the length of a piece, and it’s not officially a dado anymore, but a slot or groove.

There are multiple ways to interlock these square slots and notches, but none are as strong as the joinery types that you’ll find below. So while dadoes, rabbets, and grooves might be strong enough for built-in cabinets—with a wall behind them, a floor below, and a face frame up front—they usually aren’t strong enough as a primary joint in free-standing furniture, where they get used more for alignment and a medium measure of strength, or used in conjunction with another method, like screws.
The exception is the tongue-and-groove used to align boards edge to edge, where the long-grain glue surfaces provide all the strength you could wish for.
Splines and keys
These are both thin pieces of wood that go into a slot, usually cut with a tablesaw blade. If you cut long slots down the length of your workpieces, the long thin pieces you insert are splines. If the thin pieces are shorter, inserted across a miter joint, for example, they might be called either splines or keys.
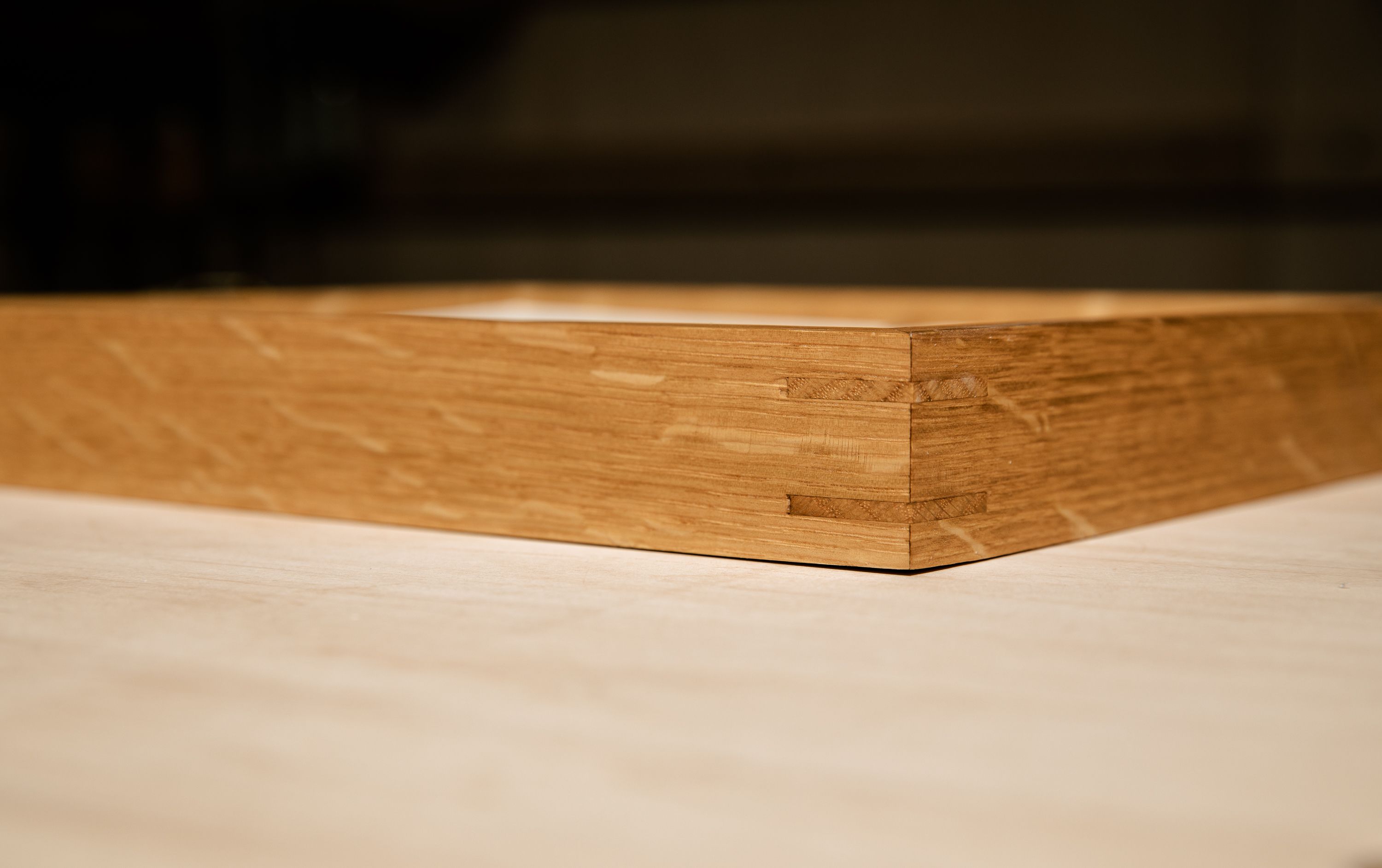
Inserted down the length of a joint, splines are a great way to avoid cutting a matching tongue and groove. Instead you can just cut a single slot on each piece. Keys can be inserted in miters in various ways, adding not just strength but also a lovely decorative feature.
As for the spline material, it depends on whether it will be visible or not. Hardboard and thin MDF make good hidden splines. Or you can cut your slots first, and then cut, plane, and/or sand solid wood keys to fit.
Lap and bridle joints
Used most often to join the ends of pieces at right angles to form some sort of frame—be it a face frame, door frame, or table base—lap and bridle joints are closely related. Cut a single notch out of each piece, allowing one to overlap the other, and you’ve got a lap joint. Cut notches out of both sides of one piece, to form a tongue, and then slot the other to fit, and you have a bridle joint.

In either case, the large mating cheeks of the joint are long-grain-to-long-grain, so they hold glue well and are extremely strong if you clamp them properly while the glue dries.
Box joints
There are many variations on the box joint, from wide, pinned joints seen in Arts and Crafts-style furniture to square, evenly-spaced box joints of the minimalist style. Used to join the ends of wide boards, to create everything from small boxes to whole cabinets, these joints feature rectangular interlocking fingers (as opposed to the angled fingers of a dovetail joint). The more fingers you have, the more long-grain cheeks there are, and therefore the stronger the joint is. That’s why the fatter tabs in Arts and Crafts-style cabinets are often reinforced with pegs.
There are as many ways to make box joints as there are variations on their pattern. Square, evenly spaced fingers are often cut on the tablesaw, using a shopmade jig that spaces and sizes them perfectly. Templates are available that make box joints easy to cut with a plunge router, although here you are bound by the pattern of the template. Finally, for the ultimate speed and flexibility in box joint production, Shaper Origin and Workstation can be combined to make a box joint powerhouse. Evenly-spaced box joints of any size are easily programmed on Shaper Origin itself, and more complex Arts and Crafts-inspired box joints can be prepared in advance with the help of a computer.
The big two
If you are joining panels of any kind—be it for a small box, a drawer, or the four sides of a large cabinet—the strongest joint is the dovetail. It interlocks like a box joint, but has angled fingers. And for any sort of frame joint—be it a chair, table base, door frame, or whatever—there is nothing stronger than a deep mortise-and-tenon. These joints tend to be the most painstaking and challenging to execute, but when you need to maximize strength and durability, they have no equals.
There are jigs and tools designed to make these joints much faster and easier to execute. Shaper Origin and Workstation are among the best. There are also dedicated dovetailing jigs, and the aforementioned Festool Domino, which lets you insert pre-made tenons into almost any panel or frame joint.
Dovetails are strong and beautiful
A row of well-crafted dovetails is a thing of beauty, making it one of the hallmarks of fine furniture. Saw and chisel them by hand, and you can execute them any way you like, with varied spacing and very narrow, elegant pins. Cut them with a router jig or other machine setup, and you can speed up the process and make a tight fit easier to achieve. For the best of both worlds, Shaper Origin and Workstation can be combined to cut dovetails using a process similar to cutting box joints.
The two parts of the joint are called pins and tails, with the tails being the part that looks like the tail of a bird, and the pin being the angled fingers that fit between the tails. And there are two basic types of dovetails, through and half-blind. Through-dovetails are exposed on both sides of the joint, and are therefore used on boxes and cabinets, while half-blinds can only be seen along one edge, making them great for drawers.
In either case, through or half-blind, think about the forces the joint will encounter when deciding how to orient pins and tails. Because of the angled interlock, the joint is much easier to pull apart in one direction than the other. For that reason, the sides of wall-hanging cabinets usually get the tails, to resist the force of gravity, and drawer sides get the tails too, to withstand being pulled in and out over the years. In most other cases, just pick the orientation that looks prettiest!
Quick caveat: While woodworkers often think that dovetails are the only way to build fine furniture drawers, there are other very strong, attractive ways to do it—such as a combination or rabbets and small dowels, or simple box joints, or Domino tenons, etc.—so you don’t need to cut dovetails to be a fine woodworker. The same goes for the debate over hand- vs. machine-cut dovetails. Non-woodworkers don’t often notice or care, so don’t get too uptight about what you choose.
Mortise-and-tenon is the king of the frame joints
Take apart heirloom furniture (if you can!) and you’ll usually find deep mortises and tenons (M&Ts). The tenon is the protruding part, usually rectangular, and the mortise is the square hole that fits it. You can make a M&T joint almost any size or depth, letting you maximize the strength of any two parts being joined together.
Another reason the M&T rules is how it can be interpreted, making it not only bombproof but also decorative. The most basic M&T has a tenon that fits into a blind mortise. This means that the tenon ends inside the mating piece. The less common through-tenon continues through the mortise and is visible on the other side. A tenon has three important elements: shoulders, ends, and cheeks. The cheeks are the broad sides of the tenon, where it meets the mortise walls long grain to long grain, and where it gets most of its glue strength. The ends are the other, narrower sides of the tenon. And the shoulders are the narrow steps formed at the base, which butt up against the mating piece, closing the joint, and making one piece appear to run cleanly into another. The mortise has walls, ends, and a bottom. The walls are the most important element for glue strength, so it’s important that the walls not be so thin that the tenon flexes them outward when inserted.
A beautiful and time-tested way to reinforce M&Ts is to drive pegs through their sides. These are seen in everything from door frames to the huge timber-frame joinery used to make houses and barns. Look up “draw boring” and you’ll find a way to drill slightly offset holes for those pegs that will actually actually draw the parts together as you drive them, and then stay there adding strength for generations to come.
Through-tenons are next level
If you cut the mortise all the way through the mating piece and send the tenon through too, you have a through-tenon, with an exposed end that offers opportunities for reinforcement and decoration. If the tenon stops flush with the outside surface, or protrudes only slightly, you can drive wedges into the end grain, adding a decorative touch and lots of added strength. If it sticks out a lot more, you can cut angled holes in the protruding ends, and drive wedges through those, with the tenon and wedges creating a gorgeous mechanical joint that will survive a tsunami. One of the huge advantages of Shaper Origin is how it can machine both mating parts of almost any type of M&T, with a perfect fit, opening up a new level of strength and beauty in your work, with speed and ease not previously possible.
All of this is just an introduction to the wonderful world of wood joinery, designed to help you zero in on the best options for your next project. Start here, and then seek out additional info on whatever you choose. Woodworking is a journey.