EVT and the Path to Production

These past several months have been all about execution. The team has been heads-down and focused on bringing Origin hardware and software to a state of production readiness. Earlier this year, we identified a capable Contract Manufacturer (CM) to partner with to assemble Origin to our specifications. Since then, much of our hardware engineering team has been embedded at the factory, where we’ve recently concluded our Engineering Validation Test (EVT) build.
EVT is an especially critical phase for any hardware development effort. It marks the first time devices are assembled with production-intent designs and manufacturing processes. This means actual production tooling (e.g. injection molds for plastic components, die-casting molds for aluminum components), production electronics and production assembly fixtures. Origin units are assembled in a manufacturing production setting, where all assembly processes are defined and refined, including factory test and calibration procedures. The build process is relatively slow compared with what we’ll expect in series production, but this is the time to trial all processes and optimize workflow.

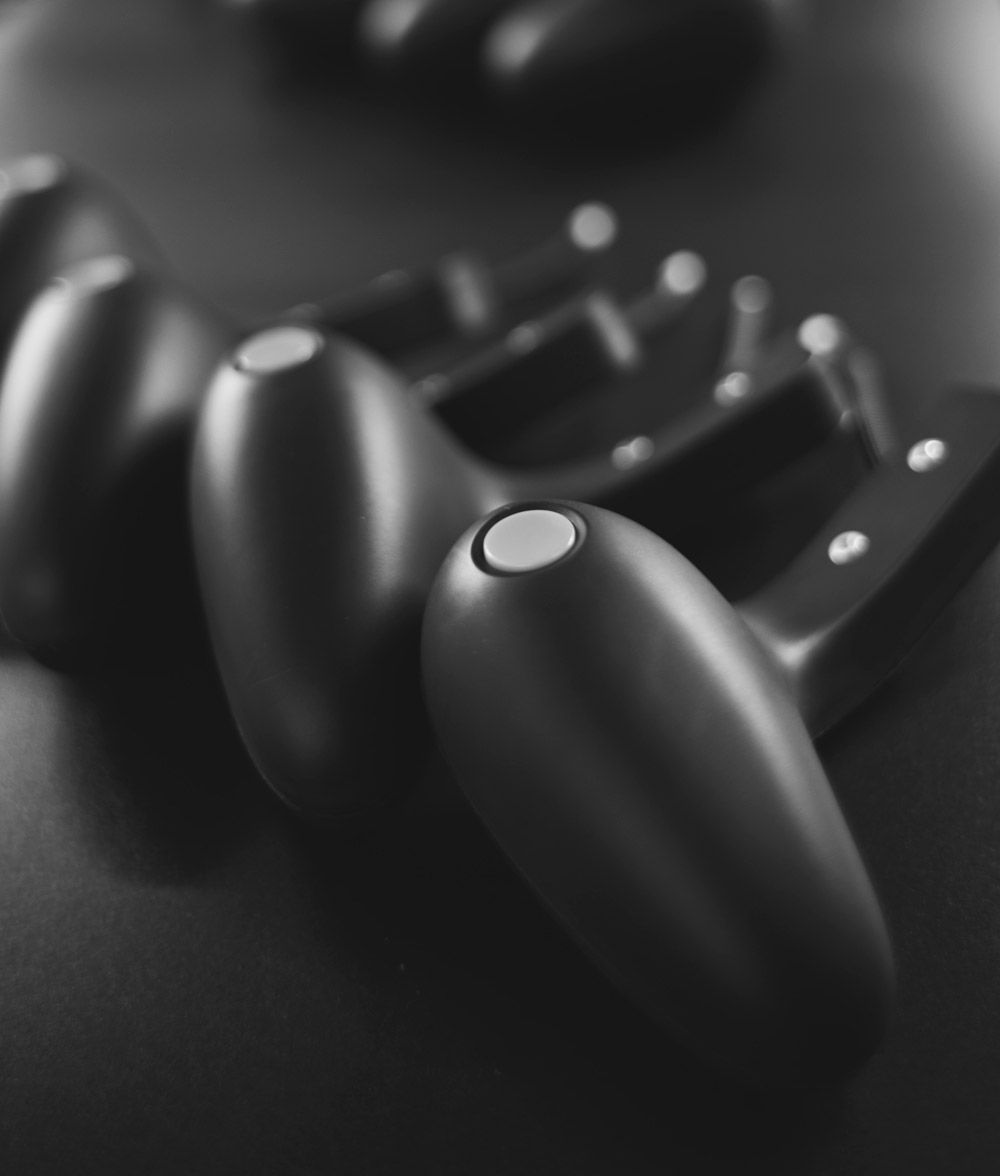

The freshly-built EVT devices will not be made available for sale. Instead, each EVT unit is slated for testing to ensure that our production design meets all design, performance and reliability specifications. In addition to product performance and reliability validation, EVT units are also utilized for FCC (wireless) certification and safety certification by a Nationally Recognized Test Laboratory. Planned testing commenced as soon as units started rolling off the assembly line, and will continue for the next several weeks. Crucially: Shaper Origin is alive and kicking. Although we’ve been beta testing our earlier hardware/software for years, and have been testing the production-intent subcomponents of the production Origin machine for many months, this is our first time merging the production-ready hardware and software together. We now have several EVT devices undergoing continuous testing in real-world scenarios.
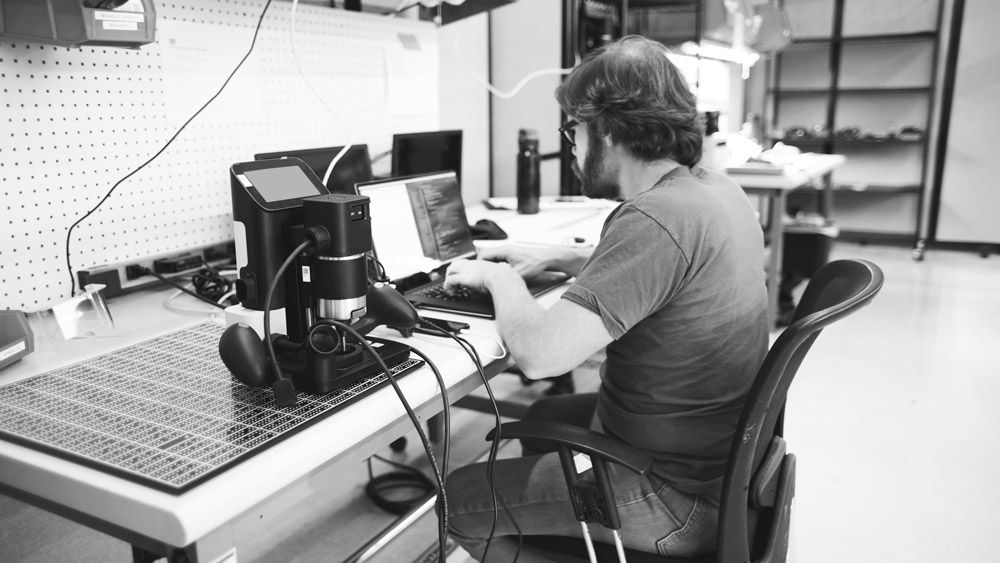
This stage of validation is critical because it allows us to gauge our production readiness, and it is one of our final chances to remedy issues that could otherwise plague product performance or manufacturing production. We’re super happy with what we’re seeing so far, and we’ve already knocked down some minor issues that only become apparent when you start to manufacture products in sizeable quantities. We have one additional validation build planned later this summer prior to ramping into production. If all goes according to plan, we will remain on track to begin Batch 1 delivery this fall.
